There are a number of AFM techniques sensitive to the local mechanical properties of a sample. However, it is still challenging to distinguish between the different properties of materials like stiffness, hardness, adhesion, and viscoelasticity on these compositional maps.
Fig.1. Force-time and force-distance curves recorded in tapping mode on high-density PE layer (a) and low-density polyethylene layer (b). Image courtesy of Ozgur Sahin (The Rowland Institute at Harvard University). |
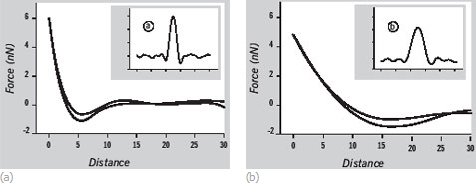 |
For selective quantitative characterization of the properties, a number of techniques have been developed. The measurements of the force curves in contact mode provide information about the local mechanical properties. The experiments can be focused on exploring stretching and rupture of individual macromolecules.
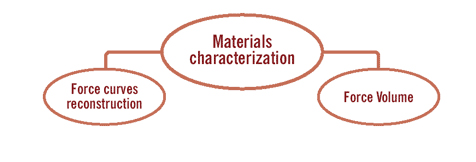
Force Volume
Force Volume imaging is an automated collection of force-curves data over a certain area. Practically, this is done by pulling the AFM probe from a surface after the AFM probe apex adheres to macromolecules or larger species lying on the substrate. A pulling experiment usually involves two types of AFM probes: regular silicon AFM probes and coated AFM probes promoting the adhesion process. These experiments are conducted at different strain rates and require large statistics due to the low yield of successful events. A rational analysis of the pulling force-curves is performed in terms of energy of individual chemical bonds.
Nanoindention
Another use of the force-curves is for indentation purposes. Indentation techniques are known in materials science for many years. They are applied for investigations of the hardness of various materials ranging from ceramics and metals to polymers and polymer composites. AFM-related nanoindentation complements these studies by providing the experimental data at smaller scale and at lower indentation forces.
The general routine for AFM nanoindentation experiments looks simple but it has a lot of hurdles to obtain the quantitative mechanical properties. The force-curves, which are recorded on one or multiple locations, can be obtained for different load levels at which the probe-induced sample deformation can be elastic, viscoelastic or plastic. After proper calibration of the optical sensitivity of the microscope, the precise determination of the AFM cantilever stiffness and the geometry of the AFM tip apex, the force curves can be recalculated into deformation versus force dependencies. The latter are used for evaluation of the elastic modulus, plastic yield deformation and other mechanical parameters.
This procedure is non-trivial because it depends on the choice of an appropriate model used for describing local deformation of different types. The existing models are mostly rational approximations rather than rigorously obtained solutions for AFM-relevant measurements. At the current stage of AFM-based nanoindentation reliable experimental data are badly needed. The use of well-characterized AFM probes (i.e. AFM probes with precisely determined AFM cantilever stiffness and AFM tip apex geometry) are an important pre-requisite of such experiments. Definite advantage is offered by HARD AFM probes with a larger AFM tip apex because the latter can be relatively easy characterized with scanning electron microscopy and they are less susceptible to damage during indenting.
Conventional AFM probe tips can be replaced by colloidal particles of glass, silica, polystyrene, different metals, etc., which can also be further functionalized. The applications include investigations of different phenomena like surface charging in fluids, polarization, hydrophobicity, and chemical forces. Use of special tipless AFM cantilevers may be convenient for attaching colloidal particles.